Getting the Most Out of Key Gas Monitoring
- Exquis Engineering
- Dec 10, 2023
- 2 min read
While some form of dissolved gas monitoring has become a standard practice for most utilities, there is still a strong reliance on the data collected from manual samples. This continuance of manual testing procedures, even in cases where there are multi-gas monitors in place, should raise the question of what purpose in the overall maintenance plan these monitors serve. To best answer this question, there are several factors to be considered, such as the type of monitoring being installed, as there is a much higher level of analytics that can be performed using the data collected from a multi-gas monitor compared to that of key gas monitoring.
How is the transformer being operated? This question is critical when determining the type of monitoring being installed as transformers, which are heavily loaded, tend to operate at thermal conditions which can cause a considerable amount of hydrogen generation and make it difficult to assess the health of the transformer on hydrogen values alone. Finally, how frequently is the offline DGA testing being performed? Typically, if samples are being collected on an annual basis, this can provide enough data to detect many of the common root cause failures, as transformers tend to show deterioration over a period of several years before failure occurs.
Monitoring is then responsible for detecting conditions that can occur suddenly between sample periods. These would include things such as partial discharge, in-tank arcing or exposure to high through-fault values. Since hydrogen is typically the leading indicator of these conditions having occurred, key gas monitoring should provide a reasonably high level of confidence that there has not been a sudden change in transformer condition since the last oil sample was collected. Therefore, this article will examine the use of key gas monitoring in conjunction with trending data from manual samples as a means of maintaining optimal transformer reliability
Hydrogen Generation
Hydrogen monitoring represents one of the earliest and most frequently used types of online transformer monitoring. This is due to its relatively low cost, ease of installation and the association of hydrogen as being an indicator of many of the common faults which occur in transformers.
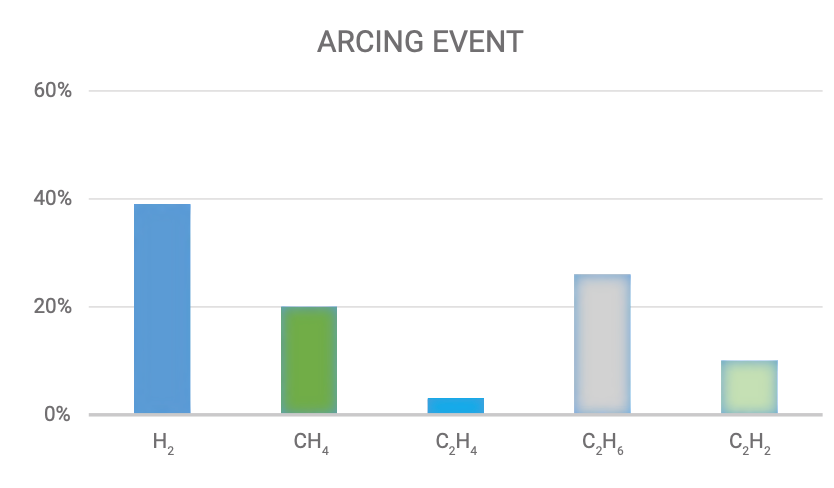
To better understand this association, an examination of the conditions under which hydrogen is produced and empirical data from case studies will be displayed. Hydrogen in transformers is produced due to a breakdown of the hydrocarbon chains which form mineral oil. This process starts when the thermal, condition within the transformer exceeds 150°C. At this point, we would begin to see hydrogen and methane molecules as a byproduct of the degradation of the temperatures increase, these methane molecules will be replaced by ethane at around 250°C, ethylene at around 350°C and finally acetylene at 1000°C.
However, despite these changes in the production of other hydrocarbon gasses, hydrogen production remains constant through all these thermal ranges. It is this consistent formation despite the thermal condition that makes hydrogen an ideal key marker for single gas monitoring. Taking that into consideration, there are several adverse conditions that can occur within a transformer of which hydrogen is a leading indicator.
By: Chris Rutledge
To download and read full article, visit https://portal.dynamicratings.com/downloads/?category=4&topic=
Comments